Silicon Solar Solutions began as a class project. Douglas Hutchings, a graduate student in the microelectronics-photonics program at the time, had always been interested in starting his own business, so he signed up for a class called New Venture Development, which is taught by business professor Carol Reeves. In this class, students are required to come up with an idea for a start-up company and write a business plan. Douglas teamed up with business students Ben Allen and Alan Perkins, and the three of them started looking for ideas.
While Reeves’ class does not require students to carry out their business plan, these three students saw it differently. “To us, the first step was having a real company,” said Hutchings. Wanting to start a high-tech company, the students began to search for technology they could commercialize.
“We were looking at tech licensing offices across the country, but could not find a good fit,” said Hutchings. “Luckily, we finally looked in our own backyard.” The students found the perfect business idea in the University of Arkansas electrical engineering department.
Hameed Naseem, professor of electrical engineering, was developing a cost-effective method of creating high-efficiency solar cells. He agreed to join the company as chief technology officer, and Seth Shumate, another microEP student, became Silicon Solar Solution’s senior scientist. The three engineers worked together to develop and test the technology, which Silicon Solar Solutions calls top-down aluminum–induced crystallization, or TAIC.
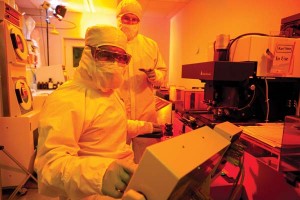
Khaja, foreground and Hutchings working in one of the University of Arkansas’ class 1000 cleanrooms.
The Technology
Most solar cells are made of silicon, which comes in two forms: crystalline and amorphous. Crystalline silicon is made up of crystal lattices, and it is very good at transporting electrons. Unfortunately, silicon made up of one uniform lattice, called mono-crystalline silicon, is expensive. Silicon made up of separate crystal grains, called poly-crystalline silicon or poly-silicon, is lower cost and easier to process. These separate grains are less efficient, however, because electrons cannot easily move across the boundaries between them. The other type of silicon, amorphous silicon, has no crystals and does not transmit electrons well.
The TAIC process turns amorphous silicon into poly-silicon with grains that measure up to 150 micrometers in diameter, while traditional solar cells have grains that measure 0.5 to 1 micrometer. These large-grain solar cells have fewer boundaries to slow down electrons, which makes them more efficient. Silicon Solar Solutions’ cells have grains that average 30 micrometers, a size that maximizes efficiency while minimizing the expense of processing them.
In addition, the TAIC process itself is more efficient than traditional manufacturing methods. Most solar cell manufacturers must add texture to their cells in order to increase the amount of photons they can absorb. Then, in order to form a p-n junction, manufacturers must diffuse boron or phosphorous onto the front of the cell, using a process called thermal diffusion. Thermal diffusion requires high temperatures—up to 1000 degrees Celsius. In addition, because this process results in diffusion on all sides of the cell, manufacturers must either isolate one side using a process called laser edge isolation, or they must remove the excess diffusion later.
In contrast, TAIC can be performed at 300 degrees Celsius and the process itself texturizes the cell, so extra texturizing is not necessary. The TAIC process is single-sided, which eliminates the need to remove excess diffusion or use laser edge isolation. These improvements result in solar cells that cost 26% less than traditional cells.
Success Stories
The business plan developed by Hutchings, Allen and Perkins has been very well received. Silicon Solar Solutions has won five international business plan competitions, and placed in the top three at six more. They have received a Small Business Innovation Grant from the National Science Foundation, a grant from the Arkansas Science and Technology Authority and $200,000 from an angel investor. In total, Silicon Solar Solutions has raised almost one million dollars in seed capital.
Hutchings explained that the company’s relationship with the university has provided a strong support structure that helped get them where they are today. In addition to the help they’ve received from faculty, the group has been able to secure access to lab and office space at competitive rates, and they have benefitted from the university’s technology licensing program, as well as the Genesis Incubator program.
Right now, Silicon Solar Solutions is focusing on testing their technology and increasing their workforce. They currently employ six people and four others are involved on an equity basis. The company has been producing solar cells for several months now, and the next step will be evaluating their cells in specific applications.
“I didn’t really expect to be here at this point,” Hutchings said about being a young CEO. “I was applying for other jobs before I graduated and I had offers that I had to turn down.” He is happy about the way things worked out, though. “This is the perfect time in life to do something like this. Otherwise you might look back years later and wonder why you never did it.”